

The enclosed chamber system is more eco-friendly because of reduced ink consumption and disposal of waste ink as well as a lower volume of cleaning solution and water required to wash-up the station for a color change.Īfter years of being relegated to jobs with low graphics requirements, flexography now rivals other printing methods for quality. Color changes are quick, speeding up changeover and setup time on a run.
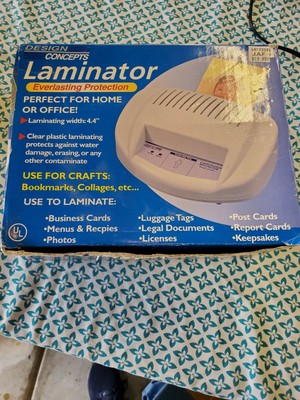
The system holds less ink than open pans, so there is not as much leftover ink at the end of a press run and ink can be removed and stored for future use.ĭue to a more efficient cleaning process, a smaller amount of cleaning solution is needed to clean up a chamber so cleaning solution waste and disposal costs are also reduced.
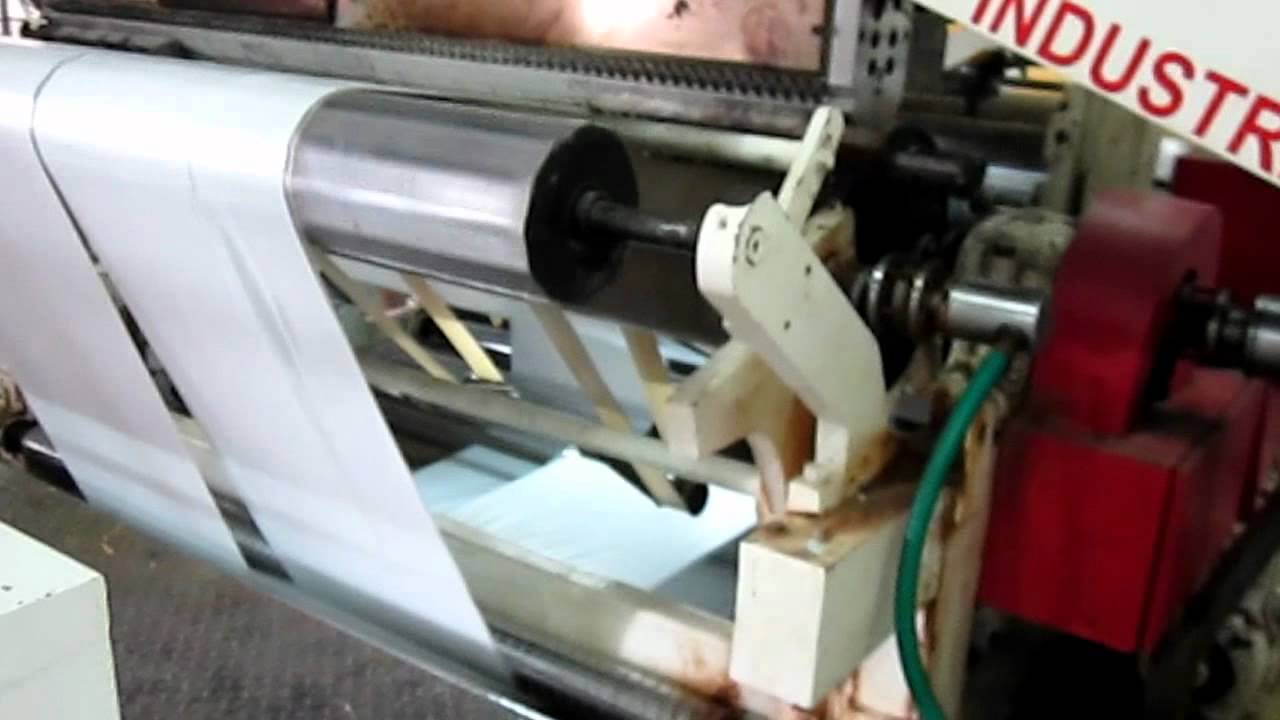
Better control over ink usage means lower ink consumption by as much as 15% per year. Also, dust, slinging and skimming are minimized. With this method, a printer can maintain ink viscosity because the enclosed design provides protection from evaporation of solvents or amines from the ink, depending on whether the ink is solvent or water-based. The ink is delivered through a closed loop from the ink pump to the doctor blade system and then back to the pump. Foam, rubber or felt gaskets seal both ends of the chamber and keep ink from leaking out. The trailing blade acts as a capture or containment blade and holds the ink within the chamber. The reverse angle blade acts as the metering blade and wipes excess ink from the anilox roll. In this system, two doctor blades are used along with an enclosed chamber to dispense the ink to the anilox roll. The most recent development in the flexographic inking process is the enclosed chamber doctor blade system. Chamber doctor blade corrugated ink delivery system Enclosed Chamber Doctor Blade System
